The opening of Molycop’s state-of-the-art cast high chrome plant in Cikande, Indonesia, has delivered substantial benefits to customers in terms of enhanced supply reliability and shorter lead times.
Key Facts
- With the opening of its cast high chrome plant in Indonesia, Molycop is perfectly positioned to meet local and regional demand for high-quality grinding media.
- The Cikande plant provides customers with high-performance cast high chrome grinding media and greater product flexibility.
- The plant enhances Molycop’s ability to deliver forged and cast high chrome grinding media directly to customers in Indonesia, other countries in Southeast Asia and Australia, reducing lead times and improving supply chain efficiency.
With the opening of Molycop’s own high chrome production plant in Cikande, Indonesia, Molycop now offers both its local customers, and customers throughout Southeast Asia and Australia, a significant supply chain advantage.
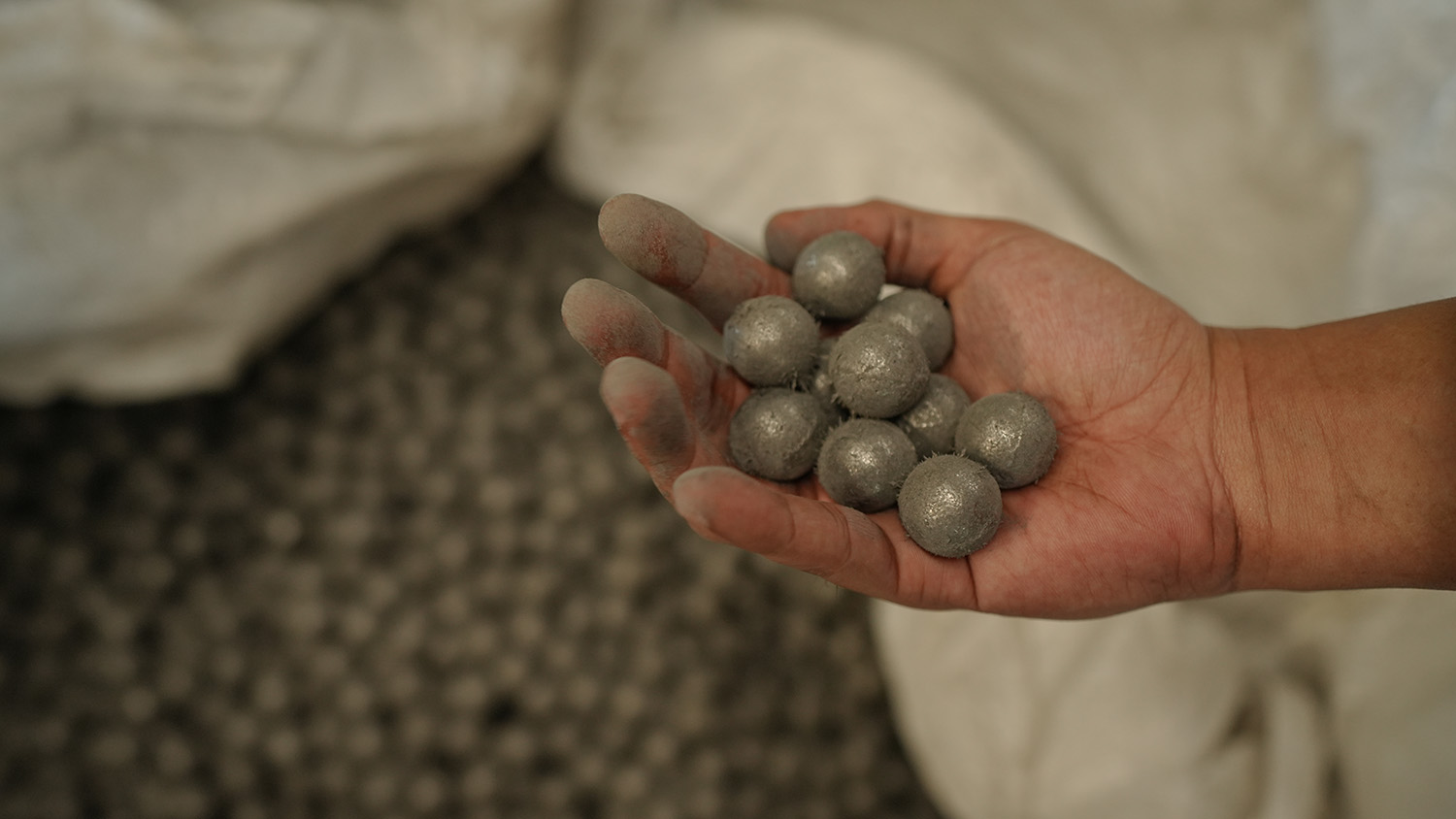
Strategically located close to Jakarta Sea port, the Cikande plant can supply mining sites in Indonesia that process copper, gold, zinc, nickel, silver and other precious metals, as well as operations across Australia, New Zealand, Papua New Guinea, Thailand, Laos, Vietnam, Philippines and Malaysia.
Here are five ways the new plant benefits operations in the region, including providing them shorter and more competitive lead times compared to their current high chrome supply options.
5 ways Molycop is streamlining the grinding media supply chain
1. Customised solutions for optimal performance
Molycop’s new high chrome plant can customise high chrome alloys specific to sites’ operational requirements. Having control over production parameters – including smelting chemistry, mold patterns, heat treatment temperatures and quenchant cooling rates – ensures that high chrome media can be tailored for individual site needs, improving grinding performance and cost efficiency.
2. Faster, localised supply
Molycop has worked diligently to increase production capacity at its Cilegon forged steel and Cikande high chrome foundries. This allows us to have enough spare capacity to support the local market as well as supplying all of Australasia. It also allows us to have product available at shorter lead times from within the country rather than the alternative supply chain challenges of importing media. It means customers have increased local inventory assurance and lead time transparency.
3. Unmatched technical support and expertise
Molycop’s experienced technical team, which includes former mining metallurgists, provides on-site support for process optimisation. Services like ore analysis, wear analysis and grindability testing help improve the efficiency and longevity of grinding media, ultimately optimising overall plant performance.
4. Cost savings with optimised alloys
With this new plant, Molycop is able to work together with local sites in Indonesia to produce both test and supply balls. Marked ball wear tests have been conducted with these optimised alloys that show increased total cost optimisation for the sites. Industrial trials with these new recommendations have also shown the customers’ potential savings in considering a local alternative with a further customised heat treatment plan.
5. Supporting sustainability and community engagement
Molycop is committed to sustainability and community engagement in the regions where we operate. Molycop's local team is proactive in working with the local community to ensure that as a local producer, we adhere to that country's production standards. This includes working with local government departments as well as ensuring we follow industry-approved safety and operating conditions. As a global producer of forged steel media for many decades, Molycop is able to adapt the same standards of production excellence and commitment to safety and sustainability to the new Cikande plant.
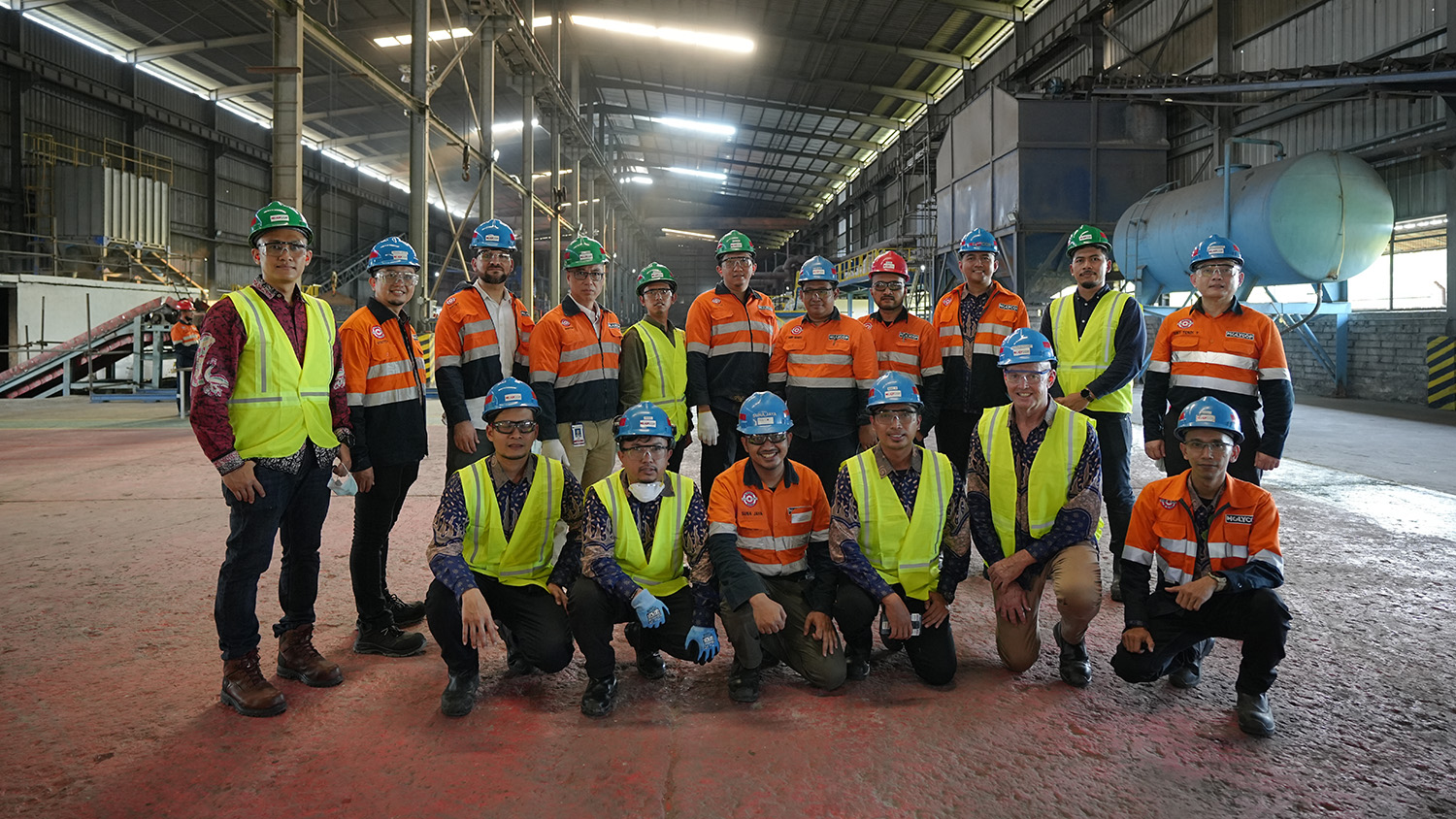
Molycop – Progress Together