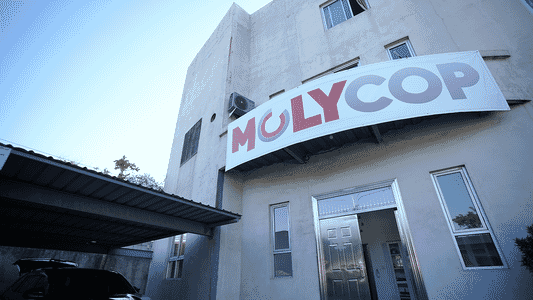
5 ways Molycop is streamlining the grinding media supply chain
The opening of Molycop’s state-of-the-art cast high chrome plant in Cikande, Indonesia, has delivered substantial benefits to customers in terms of enhanced supply reliability and shorter lead times.
Read More