The objective of a MillROC improvement project at a leading Australian nickel mine was to implement a new control philosophy around the grinding circuit, which allowed for stabilisation of key operating variables. The project led to significant improvement in circuit efficiency, reduction in energy requirements and increases in throughput.
- Improved process control strategy implemented stabilizing cyclone pressure and SAG mill weight
- As a result of the improved stability the SAG mill grate design was identified as a bottleneck and a solution presented
- Changes in SAG grate design to a combination rubber and hardox steel segments from all rubber was implemented.
Feed to the circuit is variable and comes from a range of different ore sources (underground, open pit, toll treatment) with varying characteristics in terms of competency, grade and blast fragmentation. Throughput and grind was below production targets.
In early 2020, Molycop (formerly Orway IQ) were called to the site to assist with SAG mill operation. MillROC was implemented with a live mass balance and dashboards to develop a more detailed understanding of the circuit constraints. The Phase 1 optimisation objective was to implement a new control philosophy around the grinding circuit, which allowed for stabilisation of key operating variables. Once stabilised, diagnosis of operating bottlenecks was much faster, more accurate and allowed for the implementation of some key optimisation initiatives. This identified that the circuit actually operated to relieve symptoms rather than tackling the root cause of a number issues. Once the root cause of the problems where identified and addressed, significant improvement in performance was observed.
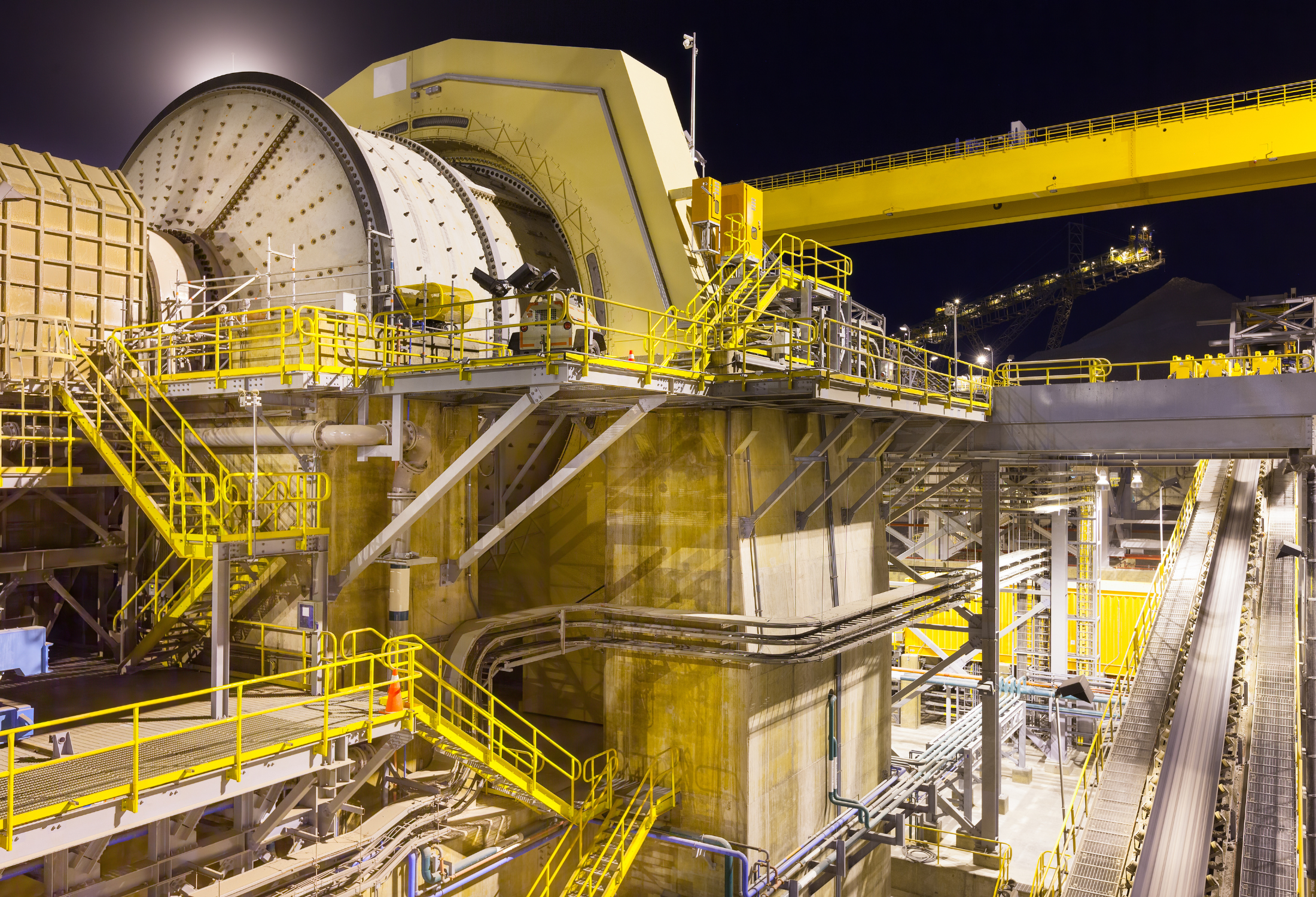.png)
The Phase 1 optimisation objective was to implement a new control philosophy around the grinding circuit, which allowed for stabilisation of key operating variables. Once stabilised, diagnosis of operating bottlenecks was much faster, more accurate and allowed for the implementation of some key optimisation initiatives